It can be a long and complex job to get a New Zealand supplemental type certificate (STC) for your new bit of kit. Here’s how it goes.
An STC is issued by the CAA to approve a design change to an aircraft, engine, or propeller. The STC approval process is overseen by the CAA to make sure all the latest safety requirements that may be affected by the design change continue to be met, and that there are no apparent unsafe conditions introduced.
Advisory Circular AC21–8 Design Changes – Supplemental Type Certificate notes that the change you want to make might have an “appreciable effect on the weight, balance, structural strength, reliability, operational characteristics, or other characteristics affecting the airworthiness of the product”.
If you’re wanting to install new equipment into or onto your aircraft, you want to know that you and your passengers continue to be safe flying in it.
So before approving an STC, the Director (or one of his delegates) needs to be satisfied that installing this new equipment won’t negatively affect the airworthiness and the safety of your aircraft.
So you have a great idea…
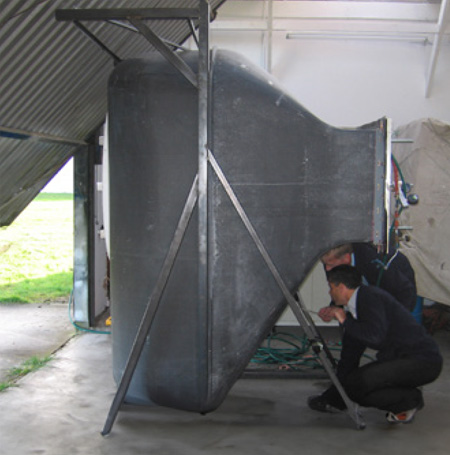
Jon Kerr and Clyde James of Part 146 design organisation, Flight Structures, doing a test article inspection prior to pressure testing a new carbon fibre hopper. This was done as part of an STC application for its installation on a P750.
Photo courtesy of Farmers Air.
You, as an individual or organisation could, legally, come up with a good idea and have the kit designed, manufactured, approved and ‘embodied’ into your aircraft.
And you could develop and complete the necessary compliance documentation and apply to the CAA for an STC yourself.
Bad idea.
The advice from every participant Vector spoke to, is to go through a Part 146 design organisation because they’re the experts. They’re dealing with STCs on a daily basis, so provide valuable guidance on the appropriate approach to the CAA for the specific design change you want to make.
Contact the design organisation early in the process and keep the communication lines open between you. Be clear about your requirements and intentions, and together with the design organisation, set goals, targets, and timelines.
Then, stay involved in the process. Know what’s happening, and what will happen next, and why. Even if the proceedings are slower than you would like, or more expensive than you anticipated, knowing why is better than not knowing what’s going on at all.
The ‘146’
The first major step in the journey to an STC is the creation of the ‘project specific certification plan’, or a PSCP. This is a core planning document that outlines what technical requirements will need to be addressed, how they will be addressed, when, and by who. The PSCP is reviewed and accepted by the CAA before the project starts, is used to plan what the CAA involvement is in the project, and what is delegated to a Part 146 organisation.
Inside the 146, there’ll be various people who have specialist knowledge to design particular changes.
Their areas of expertise might be, for example, the structure of the aircraft, its avionics systems, or its interior layout.
The design organisation makes sure the design change complies with a huge number of rules and standards (several hundred compliance requirements are common for complex projects), so the aircraft remains safe to fly, after the design change.
For instance, how does the change affect the weight and balance and the flight characteristics of the machine? What about the aircraft’s structure and airframe, the avionics, and other systems related to the changes being made?
Flight tests may be needed, as well as engineering inspections. New flight manual supplements may have to be created if there are changes to operating procedures, performance, or limitations to the aircraft. If new airworthiness limitations are needed, the instructions for continuing airworthiness may have to be changed.
The STC project may have many tasks that depend on other tasks, and depend on the availability of experts, so any delays could have knock-on effects to the entire project.
Building in some ‘fat’ and allowing for small delays in the schedule is good practice. It’s quite common to discover that changes need to be made to the design, for example after flight testing, which may create delays if not planned for. Discovering these issues and resolving them before approval is one of the main reasons why the STC process exists.
In some cases, hundreds and hundreds of documents are compiled (“…the weight of the paperwork must equal the weight of the aircraft” is a ‘joke-not joke’ in a 146) and become part of demonstrating compliance for the issue of an STC.
Finally, a Senior Person at the 146 – a Design Delegation Holder (DDH) – signs a ‘finding of compliance’, basically saying that the documented evidence demonstrates the airworthiness design standards are complied with, and, ‘acting on behalf of the Director, I can approve this aspect of the STC’.
That person is exercising a privilege delegated by the Director which takes many years of experience and training to obtain – so they’re very careful about what they’re saying.
The CAA
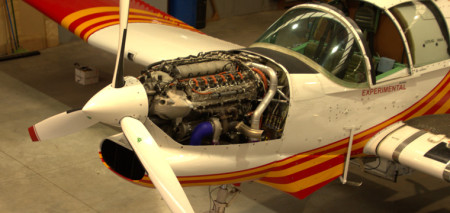
RED AO3 500HP V12 diesel engine, Phoenix Aviation Maintenance and Flight Structures. STC approval – in progress. Photo courtesy of Bill Sutherland.
The CAA’s product certification team are the ‘fresh eyes’ on the work of the 146 organisation, identifying any inconsistencies in its paperwork or methods, and querying when it’s not clear if safety requirements will be met by the design change.
Within its ranks, the team has a variety of skills gained ‘out in the field’ so it can also guide a 146 organisation, which may lack a particular area of expertise. Where the CAA team itself lacks specific experience, it reaches out to other areas of the CAA, or other regulators for guidance, such as the FAA or EASA.
Individual members of the CAA product certification team, acting on delegation from the Director, need to be satisfied of the continued safety of the aircraft, before signing off on a ‘finding of compliance’ that current airworthiness design standards are being met.
The team also needs to be confident the proposed design change meets international standards, including making sure the STC application, and the way it’s treated, is acceptable in other jurisdictions.
This standardisation is important because STCs may subsequently be validated by other aviation safety regulators for use on aircraft within their area – either directly or via the export of the aircraft.
This means the STC-holder – the operator who had the original ‘great idea’ – can sell the design change overseas.
New Zealand is a ‘State of Design’ – which means we have an engineering capability and responsibility for the airworthiness of the design changes approved in New Zealand. It means ICAO recognises that New Zealand’s manufacturing and design expertise, safety standards, and levels of compliance are such that other ICAO member states can trust what is developed here.
There are much larger ICAO member countries which do not approve designs of an aircraft from the ground up, as New Zealand does. There are much larger countries which don’t have the ability to approve originally designed and manufactured products (called OEMs – original equipment manufacturer) as this country does.
This means that aircraft designs, parts designed, and STCs from New Zealand, hold weight overseas.
The CAA sends approved design changes to overseas aviation safety authorities for validation. If those authorities find risks in the design, or gaps in the airworthiness documentation, New Zealand’s reputation is put at risk. It can also damage the commercial benefits associated with designing something that aircraft overseas can use.
The time it takes
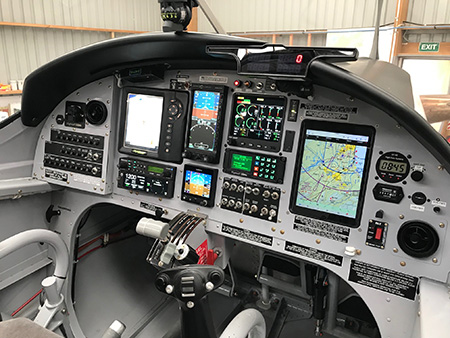
An example of a NZ CAA-approved STC – an upgrade to the cockpit of an 0800 series Cresco. Photo courtesy of Bruce Peterson.
The design change process has been described as ‘a marathon, not a sprint’. While some simple changes can be approved within months, complex innovations can take years.
Sometimes, a seemingly complex change may, in fact, be quite straight-forward to approve, and others seemingly very simple, are anything but.
The CAA product certification team and the design community say that it does take time to complete a robust design assurance process, so that you can be assured of continuing flying safety.
There’s also been a shift over the years, from aviation safety measures largely responding to an accident, to assessing the risk of an accident happening before it happens.
As a result, safety standards have become more exacting, and more emphasis is placed on understanding failure mechanisms and designing measures to prevent them from ever happening.
This is possibly reflected in the detailed information that makes up the work of a 146 organisation and the CAA. Those increasingly exacting standards over the years have also corresponded to improved global aviation safety.
If rushing an approval ends catastrophically, so too does everything else – potentially lives are lost and the assurance of safety that came with the STC is devastated. Gone, too, is all the commercial potential of the operator’s great idea.
There’s a lot riding on a properly processed supplemental type certificate.
It may be cold comfort to STC applicants who are dismayed by the length of time it takes to get an approval, but the CAA team has in fact – on numerous occasions – received praise from operators and design organisations who’ve dealt with regulatory authorities overseas, for the team’s flexibility, pragmatism, and responsiveness.
And lastly…
The STC process is detailed in Advisory Circular AC21–8 Design Changes – Supplemental Type Certificate.
Be careful about the name on the STC application. If the maintainer’s name is put down, it’s the maintainer who ‘owns’ the design change that the operator has paid for.
Advice from a well-organised maintainer
Before setting out on the path to a major modification or design change, carry out an SMS (Element 8, Management of Change) review.
Understand the change, who it will affect, identify related hazards and potential hold-ups, and plan accordingly.
If your change is new or novel, contact the CAA early. The team may not have the capability to consider the STC application, and may need to find that capability externally, or develop it internally before being able to consider the application.
Understand export control rules if you’re developing novel technology or military, dual-use technology. Passing technical information across borders can violate those controls.
With novel technology, a major modification and design change can become extremely complex. The design change activities associated with a complex STC can start to get close to the effort and cost of a type certificate.
In planning for these complex projects, use:
- Advisory Circular AC21-8 Design Changes – Supplemental Type Certificate, and
- Advisory Circular AC21-7 Product Certification – Type Certificates, specifically Figure 1: TC Process Diagram on page 8.
Not doing the design, prototype manufacture, and installation within certificated organisations can increase the conformity and compliance issues for the maintainer and operator.
New Zealand has limited access to Category 1 test pilots. This needs to be anticipated at the early stages of the project to make sure a suitably qualified pilot is available and accepted by the CAA to carry out experimental flight testing.
Before many STCs can be approved, the new design needs to be flight tested. This requires separate applications to the CAA for the Test Pilot Approval and Special Experimental Certificate of Airworthiness. The CAA wants to improve applicants’ understanding of this process and Vector hopes to run an article about flight testing later in the year.